Gadgets
How 3D-printed parts changed the NASCAR Cup Series
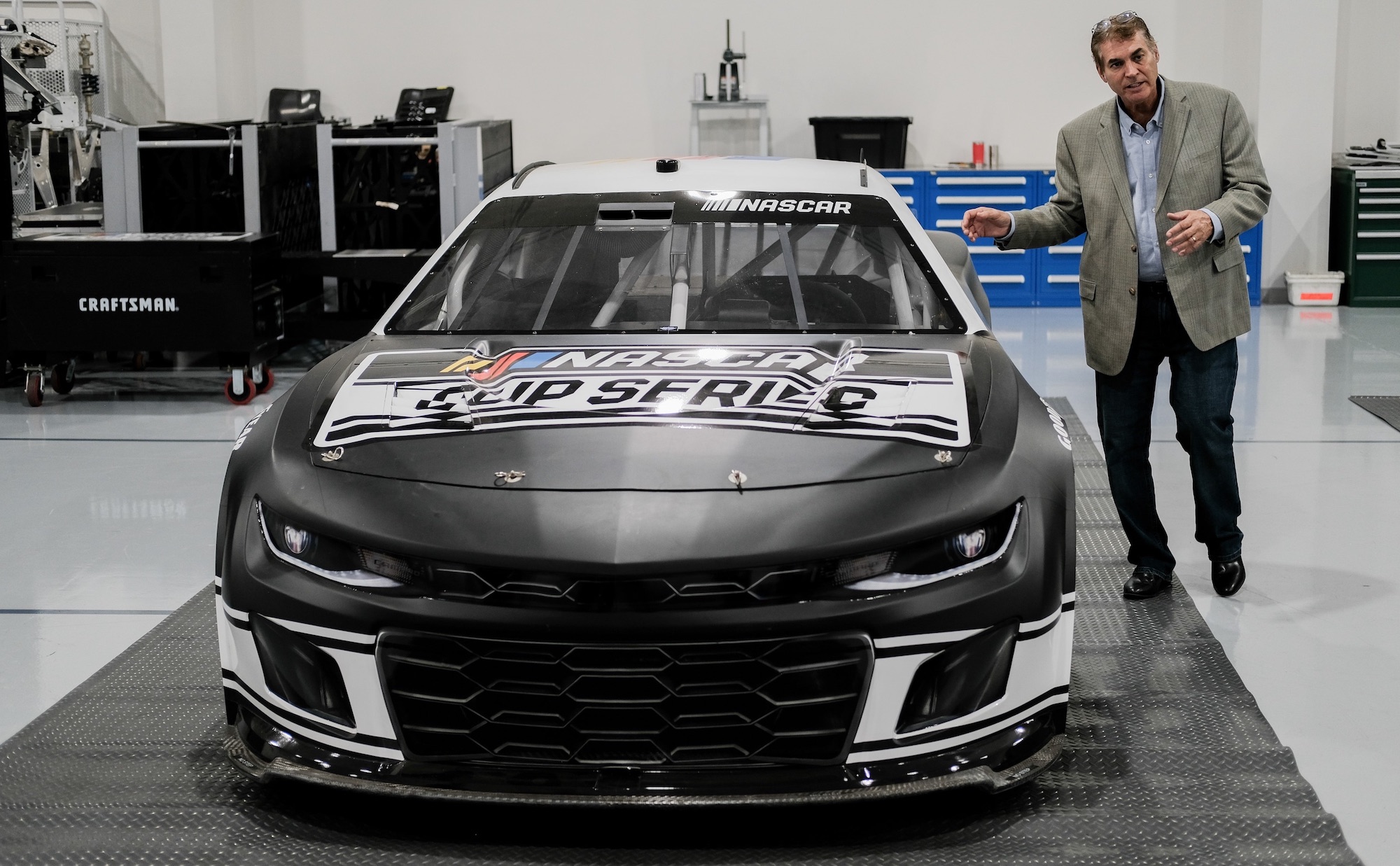
NASCAR introduced its Next Gen platform in 2021, featuring significant rule changes from its previous version. The latest NASCAR vehicles are now fully symmetrical, using composite body panels instead of metal, resembling street versions of the Chevrolet Camaro, Ford Mustang, and Toyota TRD Camry.
The Next Gen platform aims to reduce operating costs and create parity across the board in the sport of race car driving. Technique Chassis, the exclusive chassis manufacturer for the NASCAR Cup Series, produces a modular offering in three parts. This ensures that everyone starts with the same platform, with a competitive advantage found in the smallest details.
A strategic way to stand out from the competition is through the use of 3D-printed parts, representing a step up from hobbyist-level 3D printing.
Additive Manufacturing, also known as 3D printing
Stratasys, based in Minnesota, specializes in additive manufacturing, which involves creating objects layer by layer. This process is commonly referred to as 3D printing in the industry. Stratesys Senior Global Director of Automotive & Mobility, Fadi Abro, explains that additive manufacturing offers industrial-grade solutions, unlike hobby-level projects typically associated with 3D printing.
Additive manufacturing contrasts with subtractive manufacturing, which involves cutting away material to shape the final product. In NASCAR, Stratasys provides parts like ducts, covers, brackets, and tubing, working closely with the racing organization to meet driver needs and suggest modifications.

Right: 3D-printed parts on display in glass case at Stratasys.
Images: Stratasys
Previously, CNC (computer numerically controlled) manufacturing was the standard for part-making, a subtractive process that cuts material to shape the final product. Abro notes that additive manufacturing, utilized by Stratasys, offers more design freedom compared to subtractive methods.
The industrial-grade 3D printers by Stratasys are not consumer-level machines and can cost between $20,000 to $600,000 each. These printers have been used at SEMA’s annual events, showcasing 3D parts previously unimaginable.

Blazin Rods, a shop in Orange County, California, successfully used 3D printing to create the “Doughboy,” a modified 1970 Chevrolet Chevelle. The Chevelle featured custom 3D parts like carbon-fiber radiator ducts, heat exchanger outlets, air ducts, and trunk lid, leading to the vehicle winning the Best Engineered Vehicle of the Year Award from SEMA.
Stratasys has recently extended its partnership with Joe Gibbs Racing and earned the title of “Official 3D Printing Partner of NASCAR.” While competition in the 3D printing market is fierce, Stratasys benefits from its 35 years of experience and advancements in accuracy, speed, and material strength.
Abro anticipates that the next frontier in 3D printing will focus on throughput, or the speed at which printers can produce items, enabling mass customization without the need for multiple printers.
If you’re looking to increase the speed of your five to ten printers without compromising accuracy or strength, consider utilizing 3D printing technology. NASCAR, for example, values speed in all aspects of racing, and 3D printing has allowed teams like Joe Gibbs Racing to quickly test and produce new components.
For instance, when a tubing component didn’t fit properly on a JGR car, Stratasys was able to 3D print a custom fixture to address the issue. In the past, fixing such problems might have involved tedious manual adjustments or costly CNC machining, which requires skilled labor and time.
With 3D printing, teams like JGR can create ducts for airflow control more efficiently. Airflow is critical for generating downforce, cooling the engine, and even keeping the driver comfortable during races. Not only is 3D printing faster than traditional methods like milling, but it also offers cost-saving benefits and requires less manual skill.
In conclusion, embracing 3D printing for manufacturing components has proven to be a better, faster, and more cost-effective solution for NASCAR teams like Joe Gibbs Racing. It not only streamlines the production process but also ensures that parts meet the necessary specifications without compromising on quality. Can you please rewrite this sentence?
-
Destination7 months ago
Singapore Airlines CEO set to join board of Air India, BA News, BA
-
Breaking News8 months ago
Croatia to reintroduce compulsory military draft as regional tensions soar
-
Tech News10 months ago
Bangladeshi police agents accused of selling citizens’ personal information on Telegram
-
Breaking News8 months ago
Bangladesh crisis: Refaat Ahmed sworn in as Bangladesh’s new chief justice
-
Guides & Tips9 months ago
Have Unlimited Korean Food at MANY Unlimited Topokki!
-
Gaming8 months ago
The Criterion Collection announces November 2024 releases, Seven Samurai 4K and more
-
Toys10 months ago
15 of the Best Trike & Tricycles Mums Recommend
-
Tech News9 months ago
Soccer team’s drone at center of Paris Olympics spying scandal